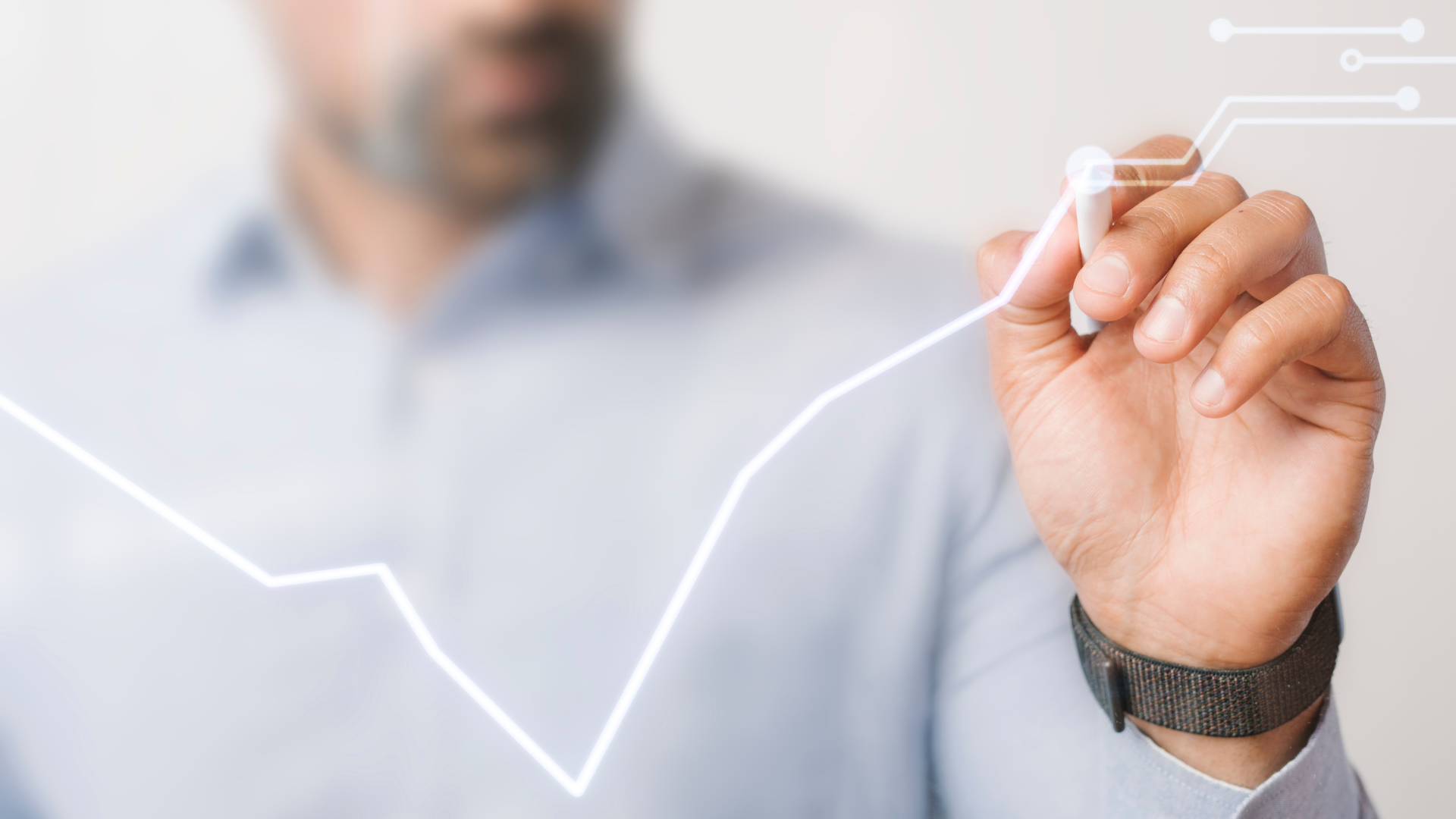
Efficiency achieved through new methods using OEE indicators
The manufacturing industry is constantly evolving, and the fourth industrial revolution has brought a wave of technological changes that are completely transforming how factories operate. The introduction of advanced technologies, such as Artificial Intelligence (AI) and Machine Learning (ML), has revolutionized the way manufacturing processes are analyzed and managed.
In this new paradigm, connectivity and data collection have become essential elements. Modern factories are interconnected, and all assets, from machines to sensors, are linked through a centralized system. This enables early fault detection, prevents unexpected downtime, and applies predictive models to improve operational efficiency.
The growing impact of Nearshoring has introduced a new competitive perspective in the manufacturing industry. Companies are striving to optimize all their processes to increase productivity and production while maintaining competitive costs. To achieve this goal, factories need to have a deep understanding of their current performance. This is where the Overall Equipment Efficiency (OEE) indicator comes into play.
OEE is a key indicator that measures the efficiency of a production line based on three main aspects: machinery availability, product quality, and machine performance. In essence, OEE provides a comprehensive and detailed view of how a factory is performing in terms of effective production time and product quality.
How to Calculate OEE:
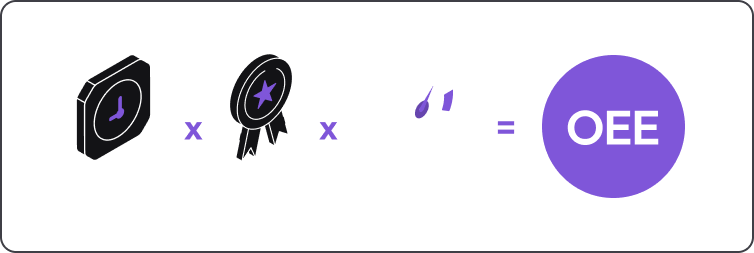
It is the multiplication of the KPIs of Availability, Quality, and Performance.
- Performance: Performance is the percentage of units a machine actually produces relative to the expected production.
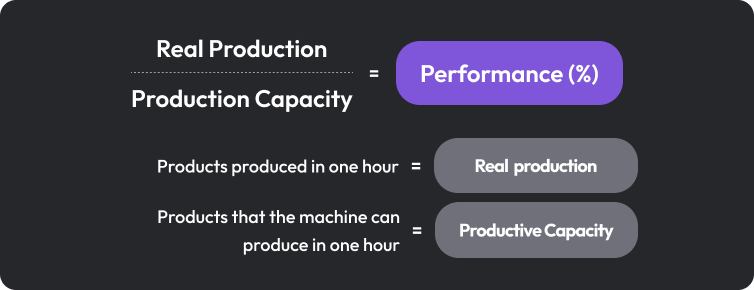
- Quality: The percentage of accepted products.

- Availability: The percentage of time the machine is working when scheduled to operate.
.png)
OEE Results:
OEE results can have a customized analysis depending on the factors influencing each production process and industry. However, the following are the generic interpretation ranges for measuring production efficiency:
- Less than 65%: Unacceptable, with significant economic losses and low competitiveness.
- 65% to 75%: Fair, with acceptable losses if the factory is in the process of improvement.
- 75% to 85%: Acceptable, with slight economic losses and moderate competitiveness.
- 85% to 95%: Good, with high competitiveness and world-class standards.
- 95% to 100%: Excellent, with maximum competitiveness and world-class standards.
At Allie, our results to date show an increase in OEE and productivity ranging from 10% to 25% in operations. We focus on advanced AI and ML technologies, collecting and analyzing the necessary data to calculate OEE accurately and in real-time. This allows companies to identify areas for improvement quickly and make data-driven decisions to optimize their processes.
Benefits of OEE with Allie's Software:
- Increase available production time: Reduce planned downtime and optimize cleaning and verification times.
- Optimize production speed and prevent interruptions: Effective planning and management of work orders to improve performance and prevent downtime.
- Reduce unplanned downtime: Early detection of potential errors and proper maintenance to minimize unplanned interruptions.
- Reduce product waste by detecting problems in the early stages of the process: Identifying and controlling critical checkpoints is essential to minimize product waste.
- Reduce cases of rejected products by effectively increasing total production.
Companies that adopt these new methodologies and technologies will be better positioned to compete in an increasingly demanding market. The future of manufacturing is changing, and those who adapt will be better positioned to lead the industry.