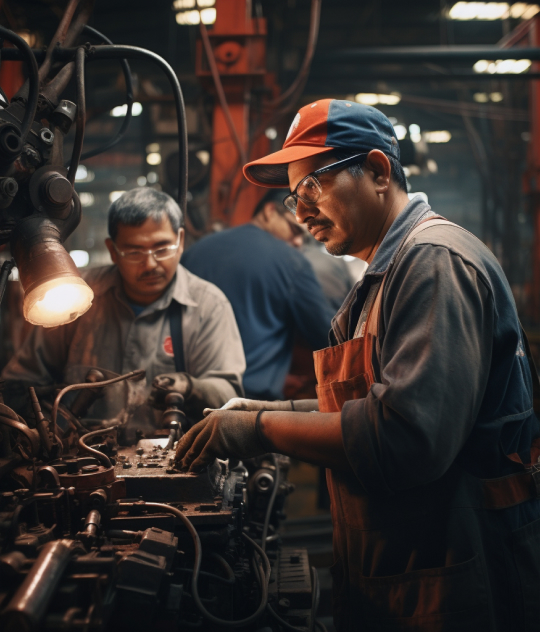
Stop Talent Drain! The Reality of Factories with a Lack of Training and How It Affects Their Productivity.
Failure to adequately train work teams in an industrial factory can have serious consequences. Firstly, it can reduce the efficiency and quality of production processes. If workers are not trained in the correct use of tools and machinery, they are more likely to make mistakes and the production process will be slower; In addition, there is a greater risk of accidents and injuries due to lack of familiarization with day-to-day processes.
Furthermore, it can lead to a negative impact on employee motivation and commitment. When workers feel that they are not receiving the training necessary to perform their jobs effectively, they may lose confidence in their abilities and feel undervalued. This generates a decrease in job satisfaction and a higher rate of staff turnover, which again correlates with the continuity and efficiency of production processes.
On the other hand, not knowing exactly the capabilities and skills of the work teams can impact the tasks within the production lines. If supervisors do not have a clear understanding of each worker's strengths and weaknesses, they may assign inappropriate or inefficient tasks, increasing production time.
With Allie, increase your productivity through the democratization of data
According to the need to centralize all information, training processes and training of new collaborators; Allie developed a special module called “People”. In it, companies can organize and have a complete overview of their collaborators, in relation to their skills, knowledge and opportunities.
One of the main features of this module is the ability to digitize the capabilities of each operator. This includes information such as experience, skills, training and certifications. With this information, production managers can assign operators to the appropriate production lines, ensuring that each line has the necessary trained and qualified personnel.
In addition, it allows companies to record the training and qualification of operators. Managers can establish specific programs for each production line and ensure that everyone is constantly updating their skills and knowledge.
Another important feature is the ability to evaluate performance. Managers can monitor and rate employee performance in real time, identify opportunities for improvement, and take action to improve operational efficiency.