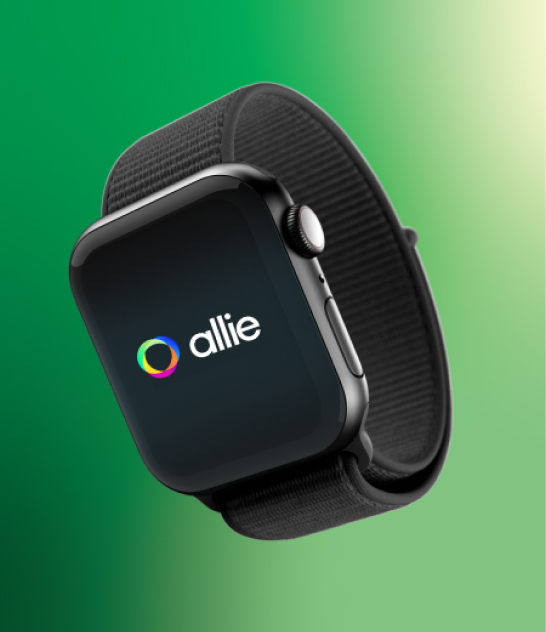
How to reduce downtime in the manufacturing industry with Industry 4.0 technologies?
For the manufacturing industry, a series of key points arise to evaluate the development of day-to-day management tasks. Reducing downtime, increasing productive capacity, optimizing asset costs, and using digital transformation to gain competitive advantage must be addressed to reach effective productivity levels.
The manufacturing industry has been experiencing growth and change at a rapid pace in recent years, and the challenges within it have grown at the same rate. The lack of complete implementation of digital transformation aggravates the situation of industries, with the most common problems being: unplanned downtime, the need for increased production, high asset care costs, and gaining an advantage over competitors. All of this can be addressed by leveraging predictive technologies already available to manufacturers.
The Internet of Things (IoT), is transforming the way production factories operate today. It allows companies to connect their equipment, machinery and sensors; to collect and analyze data in real time, allowing informed decisions to be made to improve operational efficiency and reduce costs.
One of the main advantages of IoT in production factories is the ability to collect information and perform a detailed analysis about the performance of each asset, use of resources, operational efficiency and quality in the development of raw materials; indicating problems and opportunities for improvement.
Another benefit of this type of technology is the ability to schedule preventive maintenance within the production process. Each connected sensor can detect problems before they occur, allowing companies to program actions in advance of any type of failure, reducing downtime and increasing equipment availability.
Besides, machine learning can be used to assist with early detection of machine failures by analyzing vibration and temperature data points. This can be done by training a model on a set of historical vibration and temperature data from a machine, along with labels indicating when the machine failed. Once the model is trained, it can be used to make predictions on new machine data, which can be used to identify potential problems before they cause a failure. Additionally, by analyzing the data, patterns and correlations can be discovered that can help understand the cause of the failure, which can help prevent future occurrences.
About preventive maintenance, how does it impact downtime?
Unplanned downtime has a major impact on production results and can add to global supply chain disruptions.
To reduce production downtime, factories adopting new technologies are moving away from reactive strategies, adopting preventive strategies through the use of predictive maintenance solutions. Permanently reading the information that comes from the machines, make unexpected equipment failures a thing of the past and provide unprecedented recovery capacity in the supply chain. By identifying potential problems with machinery before they lead to further failures, allows plant managers to proactively address problems, minimizing the impact on production and overall efficiency.
Maintenance software is therefore consolidated as a powerful tool that helps companies break their production records, optimize their operations and improve their efficiency. It is designed to help businesses of any size keep track of equipment and resources, schedule frequent maintenance activities, and identify and fix potential problems before they occur.
Discovering Allie
With Allie you can connect the operation, people, equipment and machinery of your factory, from a single place. We use the most advanced technology to reduce downtime and make your machines and operators more productive. Browse our efficiency, maintenance, machines and people modules.